
Yesterday, talking about my concerns about the technical limits of polyurethane resin, I anticipated how I would like to skip to plastic kits, for our (very) future releases.
Mighty Fabianowitsch, a member of our community (hi Fabian!), raised another concern about plastic pointing out legitimate reasons about the cons of plastic miniatures, and indeed I think that it might be interesting to discuss this further.
Are plastic miniatures really better than resin miniatures?
Are plastic miniatures really absolutely necessary?
I'm not an engineer nor a technical expert of plastic materials, so despite I've some knowledge about (and I'm happy to share them), take these lines as a personal opinion based on my experience as a hobbyist and creative.
I think that it's difficult, if not unfair, to claim one material better than another: it's all about context.
Resin is the best material to express our creativity, because of two main reasons:
1) This material keeps the detail of the original sculpt better than any kind of plastic or metal, allowing you to own a miniature as close as possible to the sculptor's original art.
2) Resin miniatures molds are flexible, allowing a certain level of undercuts: that means more freedom to create for the sculptor, which can make more elaborate and detailed sculpts without having to separate them into thousands of separate parts.
Resin is also enough workable, almost like plastic: it's easy to cut, sand, kitbash.
Moreover, for small manufacturers (like us), resin is economically friendly, because cost of entry is relatively low and, above all, it is perfect for limited numbers.
So you can't be surprised if almost any small/medium manufacturer produces is miniatures with this material: you can set an initial run investing a reasonable sum, and you can really enhance the quality of your creative department.
Unfortunately, it isn't all puppy and rainbows.
As I wrote in yesterday's post, the casting process of resin miniatures is highly artisanal and that means at least three things to consider:
1) times of production are really long: so for a manufacturer, especially a small one that can't invest too many funds on making a huge stock in advance, it means that you are not able to adapt to the demand of products efficiently.
2) quality standards are variable and may be affected by stupid, minor, issues that could mess up a whole stock: the mold of resin miniatures is not like that of plastic one, it is subject to a rapid wear and, for example, if the resin caster doesn't notice even small damage in the mold, all the successive copies will be damaged. I don't envy resin casters: there are so many things that might go wrong in the process, wasting hours of work and material (and money), and often is really difficult to detect them in time!

3) The economy of scale is almost inexistent. Entry cost is low, but, as any artisanal process, it doesn't get cheaper as numbers grow. If you order 30 copies, you would pay X for each miniature, and if you order 300 copies, you would pay...X for each miniature. Moreover, the more numbers you do, the more attentive you must be to point 2): quality control is crucial.
Talking about the material itself, its cons are mainly two:
1) resin is not flexible. It could be bent with a heat source, but normally if you try to bend a resin part without warming it, you will easily break it. That means that resin miniatures are more fragile than plastic ones, especially for what concerns the transport and, eventually, an accidental fall: situations that rarely happen to painters, but that are painfully frequent for gamers.
2) resin powder is not healthy. It is always better to work with resin in a well-ventilated environment, and wearing a mask because resin powder is not ideal to breathe. I suggest you sand resin miniatures using wet sand-paper, in order to decrease the amount of powder produced. With a bit of caution and common sense, resin is a safe material to work with, but we all be aware that parents might be concerned about it (legitimately).
So, here are the pros and cons of resin miniatures: I dare to describe it as an elite material, with great qualities but also with intrinsic weakness, especially for what concerns the production process.
Now, let's talk about the opponent: Plastic.
If you allow me to make a parallel that might sound racist or stereotyped but it is clearly not intended in that way (so, please, do not trigger yourselves by interpreting my words in the worst way possible!), Plastic, compared to Resin, is like Chinese industries compared to the Italian artisanal manufacturers (or at least, those ancient ones, nowadays Italy is declining more and more).
The average quality of a perfect resin cast is better compared to the quality of a perfect plastic cast, it is more defined and precious. But, despite the quality of the material is cheaper, plastic takes its strength in the highly engineered process: in the same amount of time it takes to a resin caster to make 100 perfect miniatures, a HIPS plastic machine can churn out thousands of plastic kits!
Moreover, the quality standard of the plastic manufacturing process is constant: the molds are almost eternal and their wear is laughable, so the first kit produced and the thousandth one will have the same exact quality.
For a manufacturer, this means being able to have way more firepower, concerning the production.
Moreover, plastic itself is a cheaper material, and you may consider that the raw cost of an average sprue (at least as I've been told by several contacts of Chinese manufacturers) costs less than a dollar, way cheaper than resin cost.
So, why do we keep making resin miniatures?!
Plastic process has high cost of entry: if the resin casting process is artisanal, and may involve even just a single person, a desk and some silicon, plastic is a highly engineered process and requires incredibly expensive machines and specialized workers.
That means that you can make a mold for resin production with 50/100€, but if you want to make a mold for a single HIPS plastic sprue (think about GW plastic), you have to add some zeros to the previous numbers.
Moreover, if the sculptor can almost freely sculpt a character designed to be cast in resin, when you are designing a kit for plastic production you need to be extremely more engineer and less artist because plastic molds are expensive (so you have not to waste any space of the sprue) and they allow no undercuts at all.
It's really, really, really difficult to make a plastic miniature that fits all the plastic mold requirements AND looks gorgeous: usually, to make good looking miniatures, in plastic, you need to separate them into a lot of parts, and that means more space required, increasing the already high costs of tooling.
For this reason, believe me, the modern GW plastic kits are a kind of piece of (industry) art. I really honor them. Chapeau.
Or as we say in Rome, Italy: Mecojoni! (lit: "my balls!")
So, you surely have guessed that to really benefit from plastic production, you need to make high numbers, very high numbers because you have to quickly cover the high initial costs of engineering and tooling: not our current situation, we are still making rookie numbers.
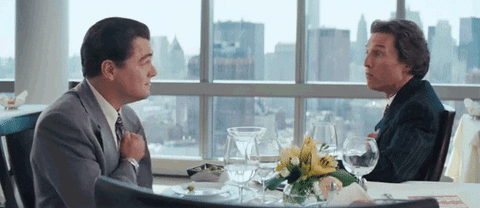
Moreover, you have to re-think your creative process, because as I said, plastic production requires a different approach to sculpting.
A LOOK AT THE FUTURE
At this point, you surely have guessed my point about the duality Resin/Plastic.
The current and future production of DPF will be based on resin miniatures, both for creative reasons and industrial ones (let's define them in this way).
We are too small to need plastic kits, we can't afford the high investments required by plastic production because we're making still low numbers (and that is perfectly normal, after all we are a newborn reality!).
Our strong point, or at least this in my opinion, lies in the creative side of our production, so to enhance it resin is still and will always be, our best friend.
However, I can't ignore the fact that, to achieve my goals, sooner or later I will have to think about plastic: I'm designing miniatures for a board game, and I think that we all agree that a game, to survive, needs to reach a vast audience.
A lot of great games are dead because of gamers that struggled to find rivals to play with, and for this reason, I think that at least the starter set of my future game (the core product) should be produced in plastic, for many reasons:
1) I should be able to distribute it all over the world to retailers and (at least it is what I would like to do) I should be able to send starter sets for free to communities and gaming associations. So I need a product that can be produced in high numbers and quickly, with a constant quality.
2) plastic miniatures are easy to transport and more resistant to classic gaming situations, so at least the core product should be the more gamer-friendly is possible.
3) with high numbers, plastic is cheaper, and that means to be able to sell the core product with a fair price (low cost of entry is my mantra when I think about my game).
I read somewhere an interview of a distributor, where he said that, for example, main distributors don't even look at KS boardgames if they don't reach at least 2000/2500 backers, and I well understand his point and, as a manufacturer, I should think about it. 2000/2500 backers to fulfill with a resin starter set would be an Odyssey, commercially speaking. Not only costs, but also times of production would be terrifying! So here is why plastic can't be ignored.
So here is my ideal situation: a core range of gaming products made in hard plastic (I would rather prefer to die and go in the Italian hell -we are obliged to eat only pineapple pizza, there-, than making my miniatures in PVC or other gummy plastics), flanked by our resin range of highly detailed miniatures.
However, before thinking about these dreams of conquers and glory, we really gotta pump those numbers.
Why not considering metal miniatures?
For what I've read around metal is a middle way between resin and plastic in terms of artistic quality and industrialization:
Moulds for metal allow some undercuts and are more durable than resin ones.
Also the costs should be way more affordable then plasic ones.